How to Find the Best Packaging Machine Repair Company Near You
How to Find the Best Packaging Machine Repair Company Near You
Blog Article
Quick and Reliable Packaging Maker Repair Service Provider to Lessen Downtime
In the competitive landscape of manufacturing, the performance of packaging procedures pivots on the integrity of machinery. Quick and dependable repair solutions are essential in alleviating downtime, which can lead to considerable monetary losses and operational setbacks. Comprehending the value of prompt interventions and the duty of specialist professionals can transform just how services approach upkeep and repairs. However, navigating the myriad choices offered for fixing services can be challenging. What factors should companies consider to ensure they are making the right selection for their functional demands?
Significance of Timely Services
Timely repair work of packaging machines are crucial for keeping functional efficiency and lessening downtime. In the busy atmosphere of production and product packaging, also minor malfunctions can cause substantial delays and productivity losses. Resolving issues promptly makes certain that makers run at their optimum ability, therefore securing the circulation of procedures.
In addition, prompt and routine upkeep can prevent the escalation of small problems right into significant break downs, which frequently incur greater repair costs and longer downtimes. A positive technique to machine repair not just maintains the honesty of the devices but also enhances the general reliability of the production line.
Additionally, prompt repair services add to the longevity of product packaging machinery. Makers that are serviced quickly are less likely to deal with excessive wear and tear, enabling organizations to maximize their investments. This is especially crucial in sectors where high-speed product packaging is vital, as the demand for regular efficiency is vital.
Benefits of Reliable Company
Dependable solution companies play a crucial role in ensuring the smooth procedure of product packaging equipments. Their know-how not just improves the performance of fixings however additionally adds substantially to the long life of devices.
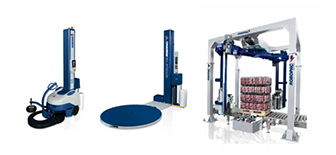
Furthermore, a trusted provider offers detailed assistance, including training and support for personnel on device operation and upkeep ideal methods. This not only empowers workers yet additionally cultivates a society of safety and efficiency within the organization. Overall, the advantages of involving dependable company prolong past immediate fixings, positively affecting the entire operational process of packaging procedures.
Typical Product Packaging Machine Concerns
In the realm of packaging procedures, numerous problems can compromise the performance and performance of makers. One prevalent problem is mechanical failure, usually stemming from deterioration or poor maintenance. Parts such as motors, belts, and equipments might stop working, leading to failures that stop manufacturing. An additional typical issue is misalignment, which can trigger jams and uneven packaging, influencing item quality and throughput.
Electric issues can also disrupt product packaging procedures. Defective circuitry or malfunctioning sensors might cause irregular equipment habits, creating hold-ups and increased operational costs. Furthermore, software application problems can prevent the equipment's programs, causing functional ineffectiveness.
Inconsistent item circulation is one more important problem. This can emerge from variations in product size, weight, or form, which might influence the equipment's capability to deal with items accurately. Finally, not enough training of drivers can worsen these issues, as untrained employees may not acknowledge very early indications of malfunction or may misuse the devices.
Addressing these common packaging equipment issues quickly is necessary to keeping productivity and making certain a smooth operation. Regular assessments and positive maintenance can significantly alleviate these concerns, promoting a trustworthy product packaging environment.
Tips for Lessening Downtime
To decrease downtime in product packaging procedures, implementing a proactive maintenance approach is vital. Frequently set up upkeep checks can determine possible concerns before they escalate, making certain devices operate successfully. Developing a regimen that includes lubrication, calibration, and inspection of critical parts can substantially decrease the regularity of unexpected failures.
Educating staff to operate machinery see this here appropriately and recognize early warning signs of breakdown can additionally play an essential duty. Empowering drivers with the knowledge to carry out fundamental troubleshooting can protect against small problems from creating significant delays. Preserving an efficient stock of essential spare components can expedite fixings, as waiting for parts can lead to extensive downtime.
Furthermore, documenting machine performance web link and upkeep activities can assist recognize patterns and recurring issues, enabling targeted interventions. Integrating sophisticated surveillance modern technologies can offer real-time data, enabling anticipating maintenance and minimizing the risk of sudden failures.
Lastly, promoting open interaction in between operators and maintenance groups makes certain that any kind of abnormalities are quickly reported and attended to. By taking these positive actions, businesses can boost operational performance and considerably minimize downtime in product packaging procedures.
Picking the Right Repair Work Service
Selecting the proper repair solution for product packaging devices is a vital choice that can significantly impact operational effectiveness. A well-chosen solution provider ensures that your equipment is repaired promptly, effectively, and to the highest possible requirements. Begin by reviewing the service provider's experience with your particular sort of packaging tools. A service technician accustomed to your equipment can detect issues extra accurately and apply solutions a lot more swiftly.
Following, think about the company's credibility. Seeking comments from various other services within your market can give understandings into reliability and quality. Qualifications and partnerships with identified equipment producers can additionally indicate a dedication to excellence.
Additionally, assess their action time and availability. A service copyright that browse this site can offer timely assistance reduces downtime and keeps production flow steady. It's likewise critical to ask about warranty and solution warranties, which can mirror the confidence the copyright has in their work.
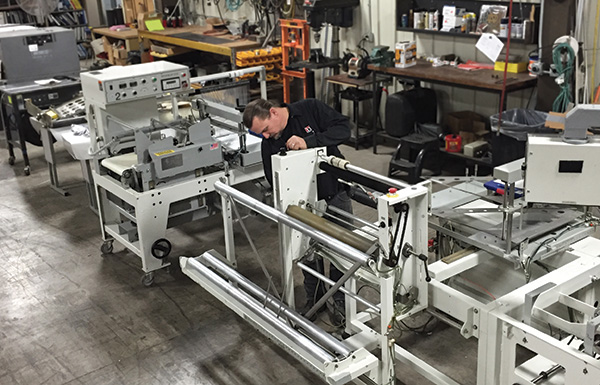
Verdict
In verdict, the value of reliable and fast product packaging device repair work solutions can not be overemphasized, as they play an essential role in decreasing downtime and ensuring functional performance. By focusing on timely repair work and choosing trustworthy solution suppliers, businesses can properly preserve and resolve usual issues productivity. Applying proactive maintenance practices and buying team training further enhances the longevity of product packaging machinery. Inevitably, a calculated technique to repair solutions fosters a more resilient manufacturing atmosphere.
Prompt fixings of packaging devices are important for maintaining functional performance and reducing downtime.Additionally, prompt repair services contribute to the durability of packaging equipment. Generally, the benefits of engaging reputable solution suppliers prolong past immediate repair work, positively impacting the entire functional process of product packaging procedures.

Report this page